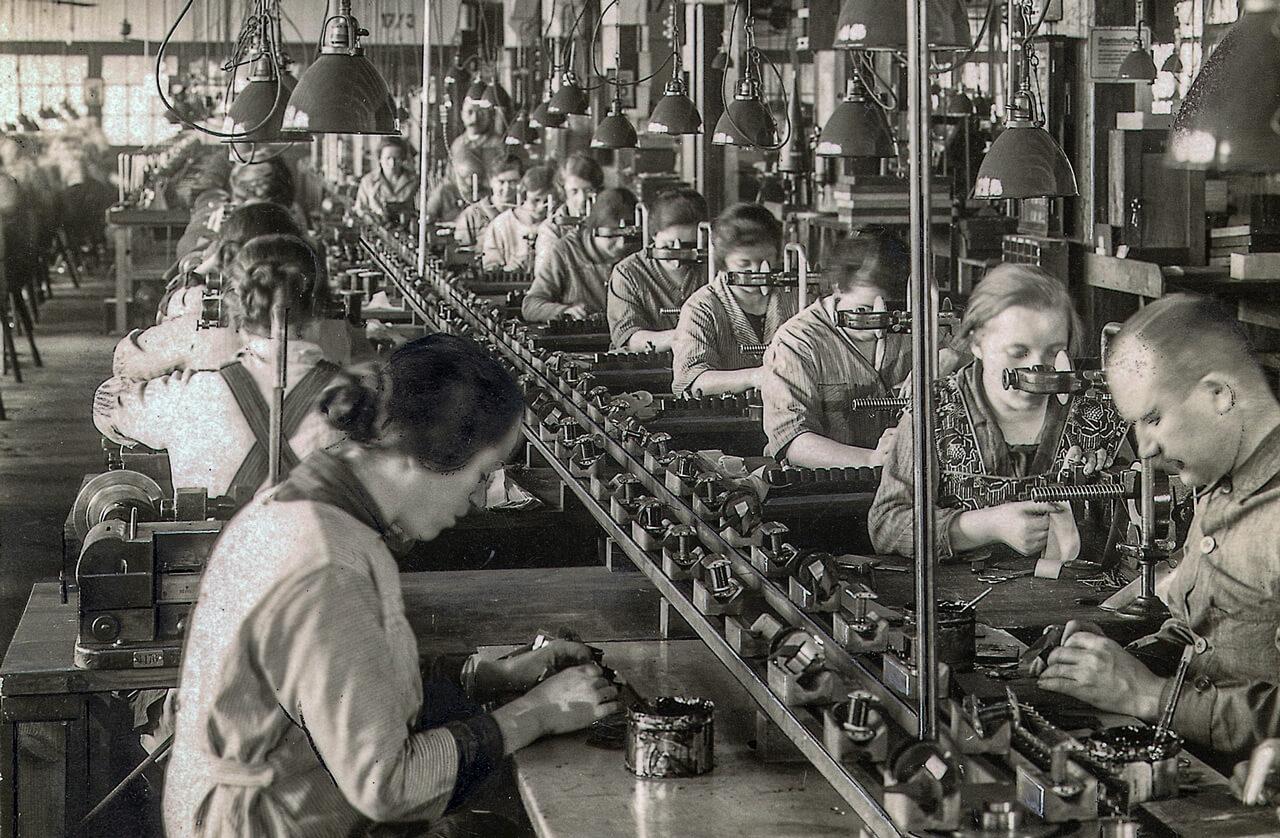
Ahogy mindenhol, kezdetben a Bosch üzemeiben is mindent kézzel szereltek össze. Ma már robotok és automatizált gyártósorok segítik a munkát, mégsem lett kevesebb munkavállaló, sőt. A vállalat 130 éves autóipari története során sok minden változott, kivéve egyet: mindig a legkorszerűbbnek számító megoldások alkalmazására törekedtünk.
Robert Bosch már a kezdetek kezdetén felismerte, hogy az innovatív gyártási technológia a kulcs a versenyképesség megőrzéséhez. Ennek a köszönhetően a munkafolyamatok, gépek és a gyártáshoz használt egyéb berendezések, eszközök folyamatos fejlesztése régóta része a vállalat stratégiájának.
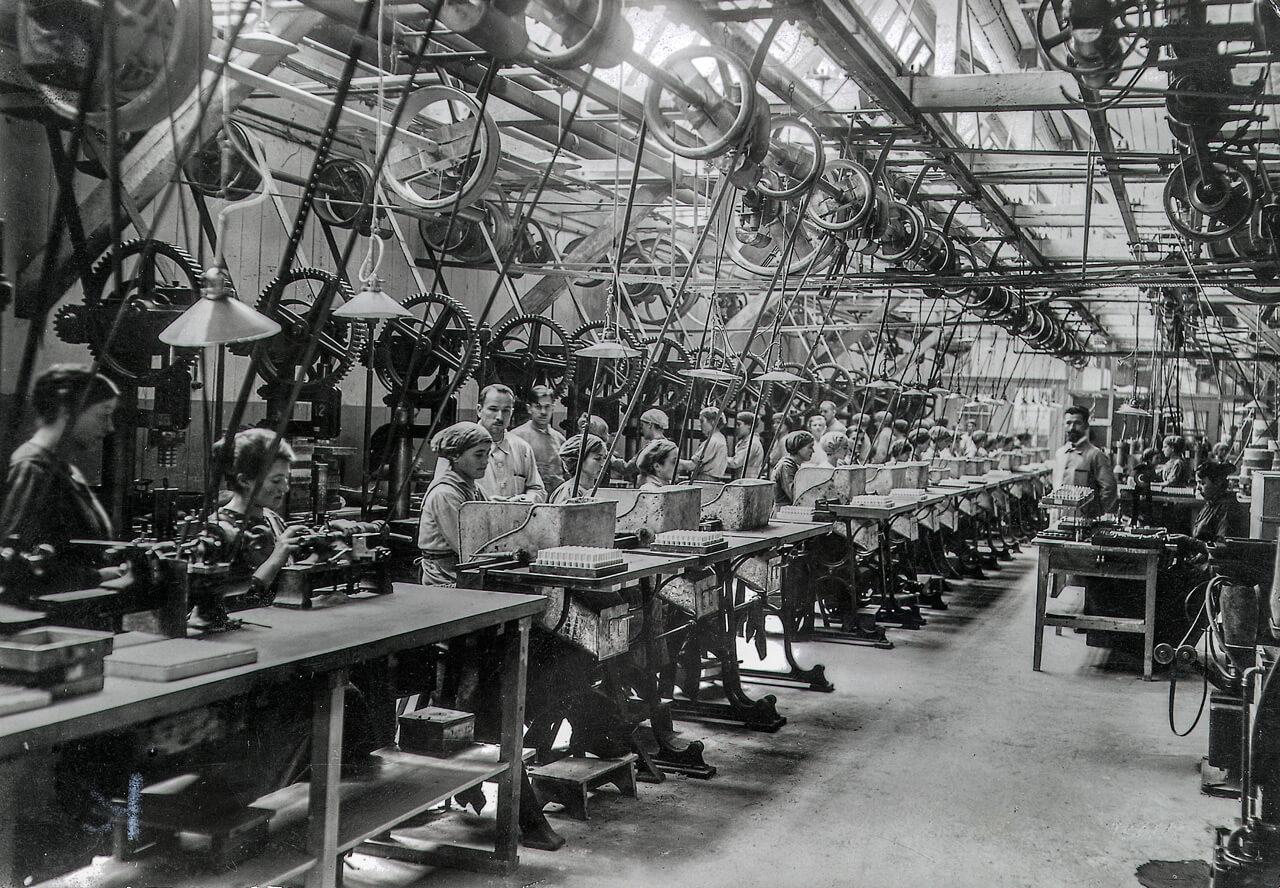
Ugorjunk vissza a jelenbe
Egy kisméretű, önvezető mobil robot (AGV) megközelíti a munkaállomást, hogy alkatrészeket szállítson. Tovább gurul a következő állomáshoz, miközben szépen kikerül mindent és mindenkit, aki az útjába esik. Az AGV megáll közvetlenül egy Bosch munkatárs mellett és ellátja a további munkához szükséges anyagokkal. Mivel a műhelyben található összes gép hálózatba kapcsolt, a gyártó egység önállóan tudta megrendelni az új kellékeket, ráadásul minden termelési és logisztikai adat valós időben érhető el.
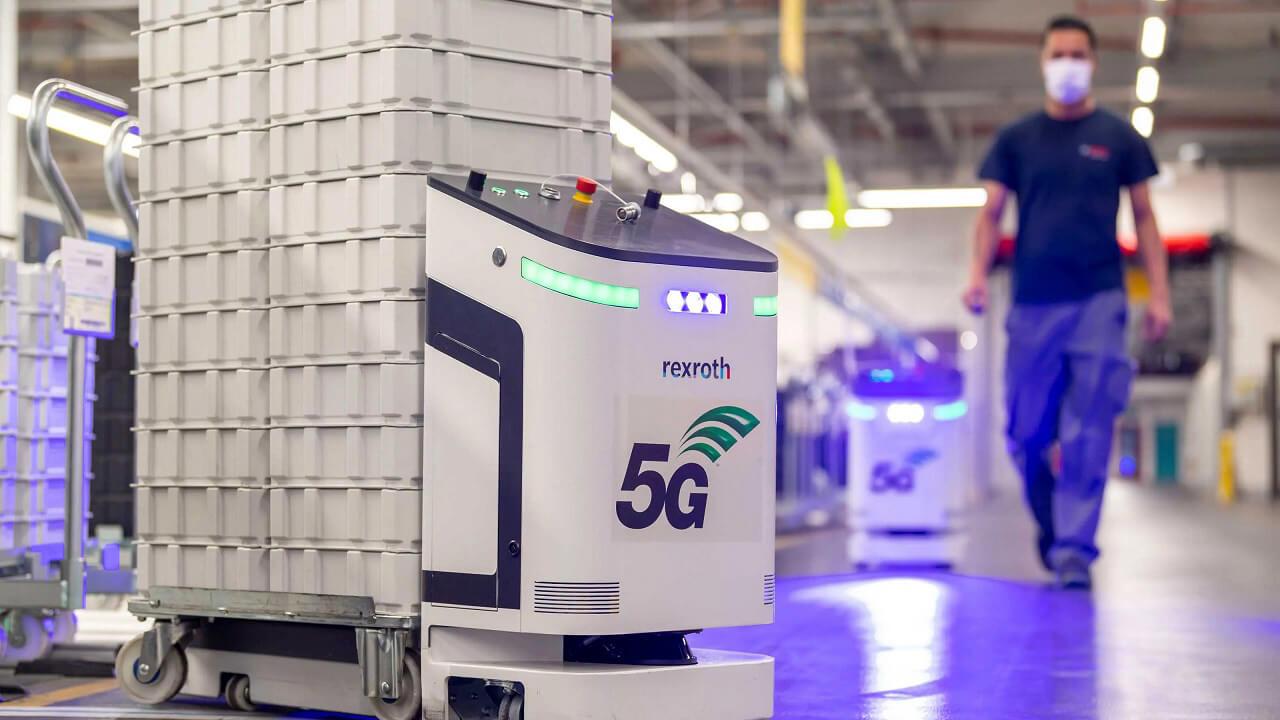
A fenti jelenet nem egy jövőben játszódó, tudományos-fantasztikus filmben látható, hanem csupán egy átlagos munkanap a Bosch Stuttgart Feuerbach városrészében lévő üzemében. Ott ugyanis 2020 novembere óta folyik a termelés a vállalat első 5G campus hálózatának használatával. Ez egy helyi mobilhálózat, amelyet az ipari kommunikáció igényeihez igazítottak, és a korábbinál még egyszerűbbé teszi a teljes gyártási hálózat kezelését. Nem csupán gazdaságos, de fenntartható és műszakilag is rugalmas ez a megoldás. Ráadásul jelenleg ez az elérhető legkorszerűbb technológia.
Mindenki csinált mindent
Kicsit több mint 130 évvel ezelőtt, amikor Robert Bosch Precíziós Mechanikai és Villamosmérnöki Műhelyében megkezdték a termelést, még egészen másképp néztek ki a dolgok. A munkanap kezdetén kiosztották a technikusoknak és szerelőknek az adott napra rendelt feladatokat. A munka nagyon változatos volt, az egyszerű precíziós-mechanikai javításoktól az összeszerelésig több dologgal kellett foglalkozniuk. Ha sürgős megrendelések érkeztek, még az is előfordult, hogy a főnök visszahívta az ügyfél telephelyén dolgozó munkatársait a műhelybe – a kollégáknak néha emiatt gyorsvonattal kellett visszautazniuk. Ráadásul ekkor még előfordulhatott, hogy egy mérnök az egyik nap még egy generátort tervezett, másnap viszont egy hűtőgépen, vagy kéziszerszámon dolgozott.
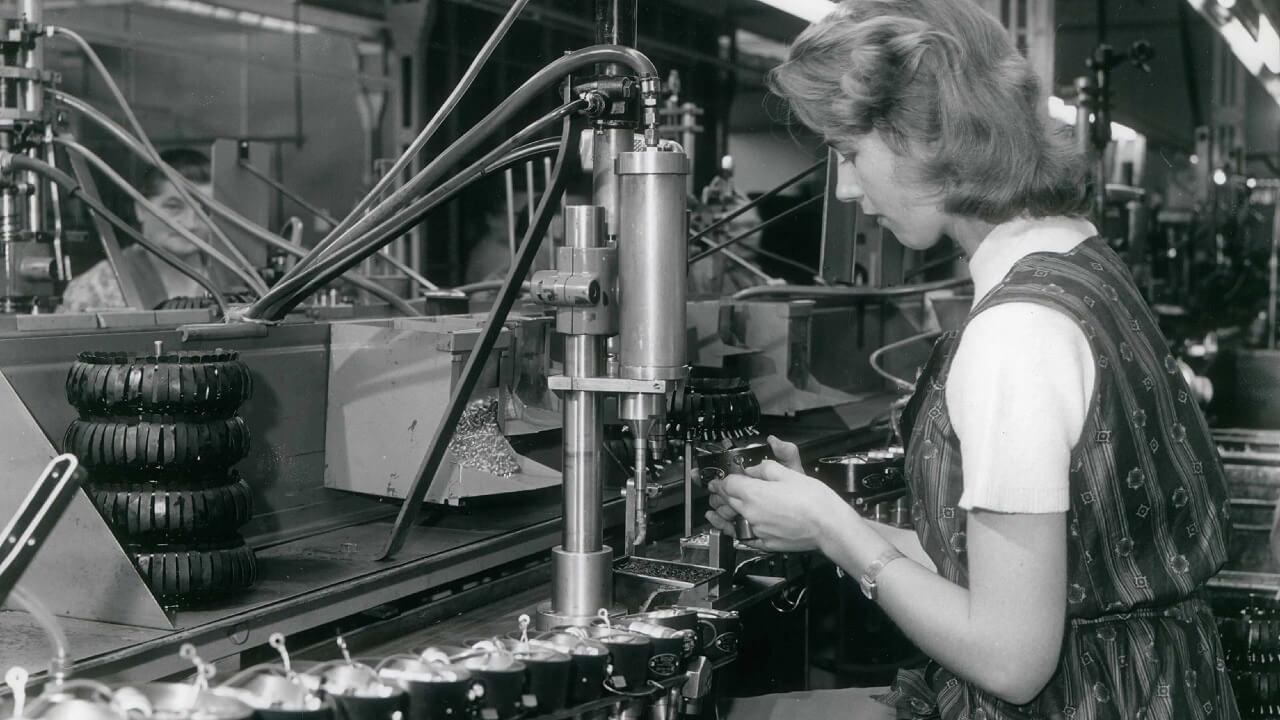
Kell valami gyorsabb
Robert Bosch kezdettől fogva nagyon figyelt arra, hogy műhelye gépekkel és szerszámokkal egyaránt jól felszerelt legyen. Szilárd meggyőződése volt ugyanis, hogy a megfelelő felszerelés elengedhetetlen a kiváló minőségű termékek előállításához. A cég első nagy sikerének, az autók mágneses gyújtószerkezetének megbízhatósága rögtön bizonyította is, és hogy igaza volt. Mivel a tudás házon belül is megvolt, a vállalat mesteremberei gondoskodtak arról, hogy szükség szerint speciális gépeket és berendezéseket gyártsanak annak érdekében, hogy gyorsabbak és hatékonyabbak legyenek.
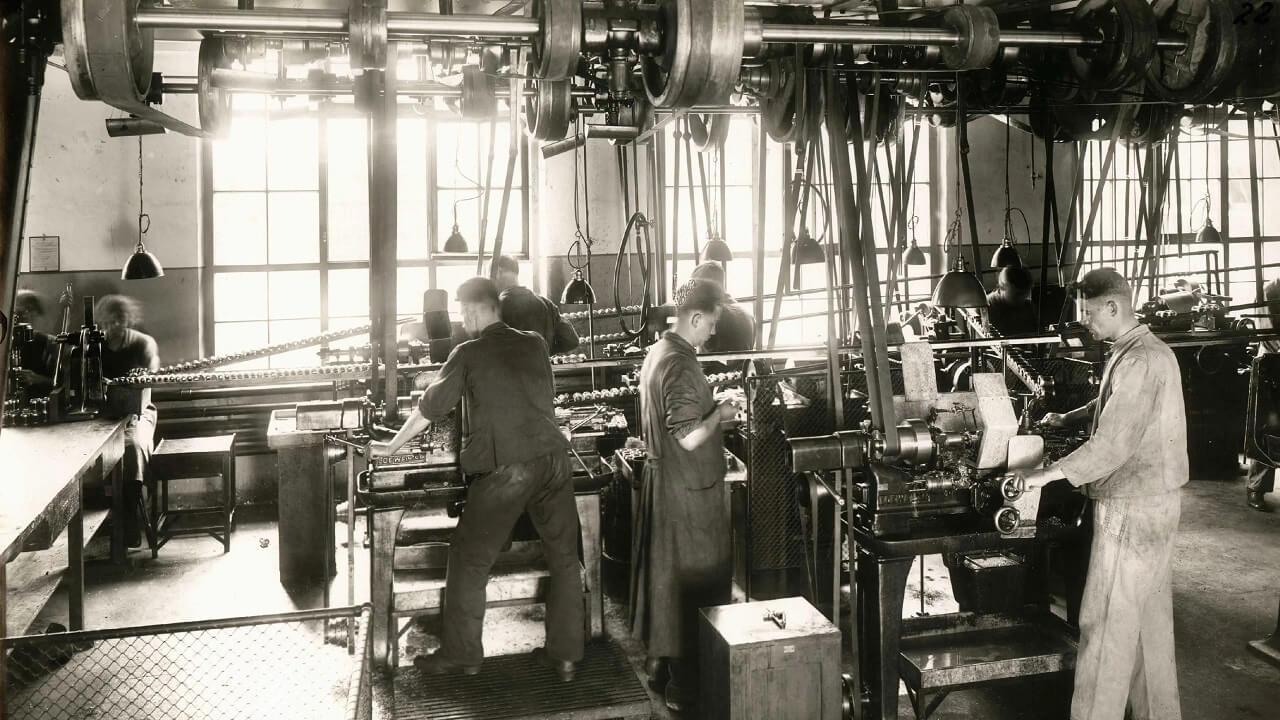
Ennek eredményeként az ipari technológia az 1900 utáni években lépett be először a vállalat életébe. Míg a legtöbb technikus továbbra is kézzel készítette az egyes termékeket, a mágneses gyújtórendszerek iránti kereslet hirtelen megnövekedése megnehezítette a nagy mennyiség gyártását a szokásos módszerekkel. Ezért ki kellett találni valami újabb, korszerűbb megoldást.
Amerikából jött az ötlet
Az autóipar válsága az 1920-as évek közepén szintén komoly kihívás elé állította a céget, hiszen még nagyobb szükség volt arra, hogy gazdaságosan, költséghatékonyan végezzük a termékek előállítását. A megoldás nem váratott sokáig magára, a Bosch akkori igazgatója, Max Rall ugyanis éppen az Egyesült Államokban tett látogatást. Arra volt kíváncsi, ott milyen módszereket alkalmaznak? Rallt egyszerre lenyűgözte és riasztotta a Ford futószalagos technológiája, ahol a személyzet az európai viszonyokhoz képest nyaktörő sebességgel dolgozott, naponta 8000 generátort készítettek.
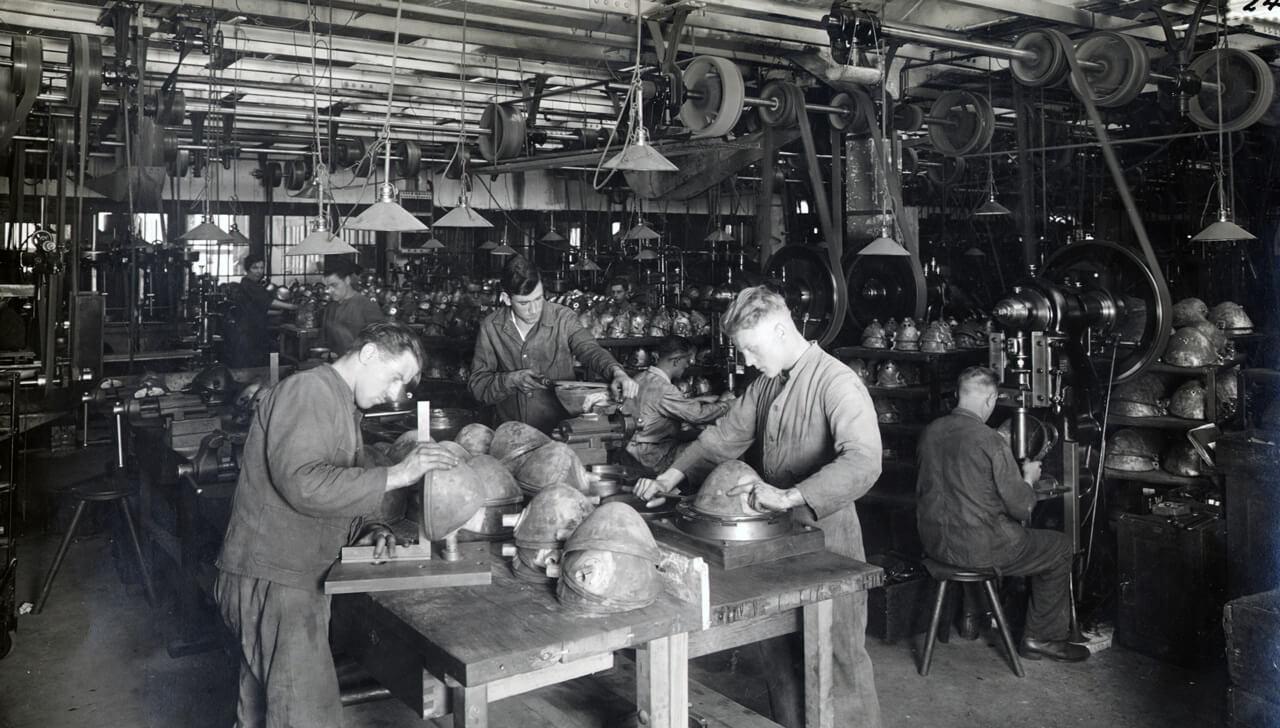
A riadalom helyét átvette a kreativitás és nem sokkal később, sok hatékonyságot és munkakörnyezet barát intézkedést bevezetve, a Bosch is összeszerelő soros gyártásra váltott. Ezzel pedig időt és pénzt takarított meg a vállalat, ráadásul egyre több munkavállalót tudott foglalkoztatni.
Jönnek a robotok
Az új, folyamatosan fejlesztett gépek és a személyre szabott munkafolyamatok lehetővé tették a termelés racionalizálását. Az ipari technológia újabb, jelentős lendületet kapott a mikroelektronika fejlődésének köszönhetően a hatvanas évek végétől. Az elektronikus vezérléstechnika kezdetben segített a nagyüzemi gyártás optimalizálásában, ipari robotokat kezdtek alkalmazni a műhelyekben, hogy elvégezzenek olyan fáradságos és monoton feladatokat, mint a hegesztés vagy a festés. Később pedig már az lett a cél, hogy ezeket a robotokat a gyártási és összeszerelési folyamatba végleg integrálni lehessen.
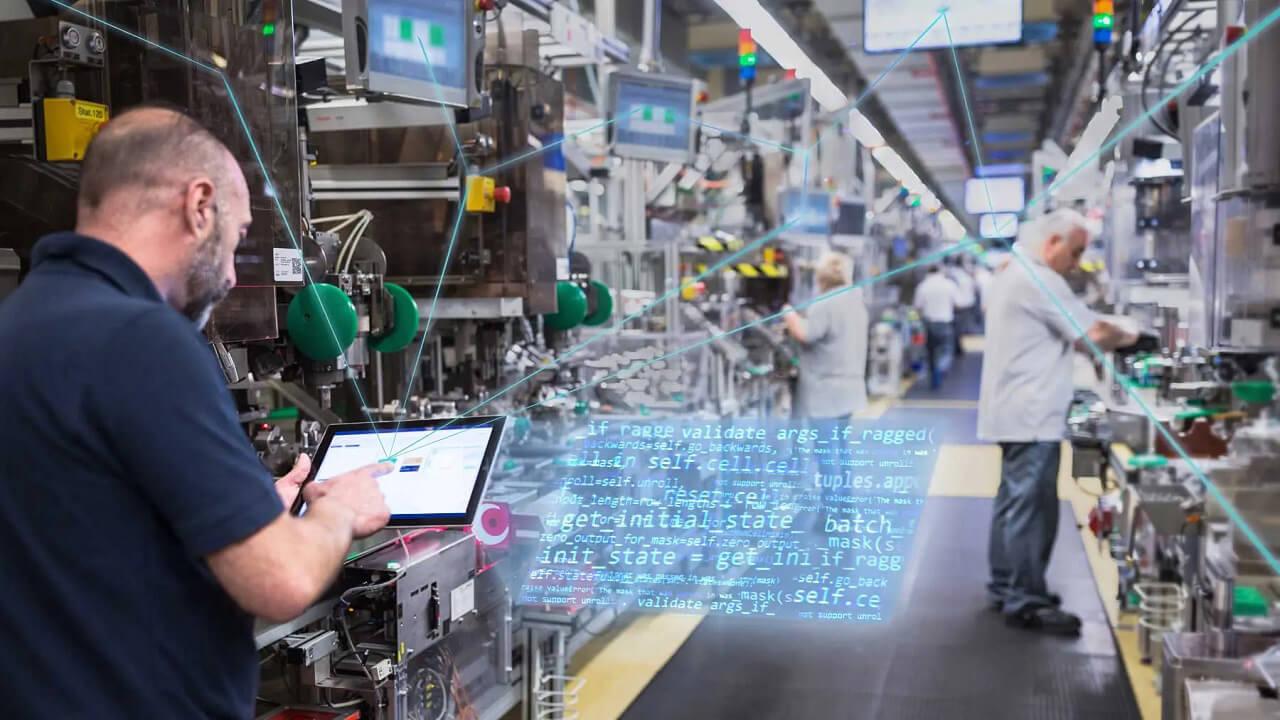
Rugalmas rendszer
1980-ban a Bosch bemutatta rugalmas összeszerelési rendszerét. Gondoljunk csak bele, Európa nagy részén az olajválság után ekkor újra fejlődésnek indult a mobilitás, az autógyárak pedig növelni tudták a termelésüket. A program moduljai a lehető legnagyobb szabadságot kínálták az ügyfeleknek, és lefedték az összeszerelési feladatok teljes spektrumát. A modulok szükség szerint kombinálhatók voltak egymással, az átviteli rendszerek szállították a munkadarabokat a szalagok hálózatán keresztül. Az ergonomikus kialakítású kézi munkaállomások ugyanúgy részét képezték a gyárnak, mint a programozható egy- és többtengelyes robotegységek. Emellett persze használtak más megoldásokat is, például szabványosított állványokat, munkaasztalokat, elektromos berendezéseket és olyan szoftvereket, amelyek a teljes folyamatot képesek irányítani. A kezdeti pánik, aminek fő üzenete az volt, hogy a robotok elveszik az emberek munkáját, szép lassan elcsendesedett, hiszen a gyárakban egyre többen dolgoztak.
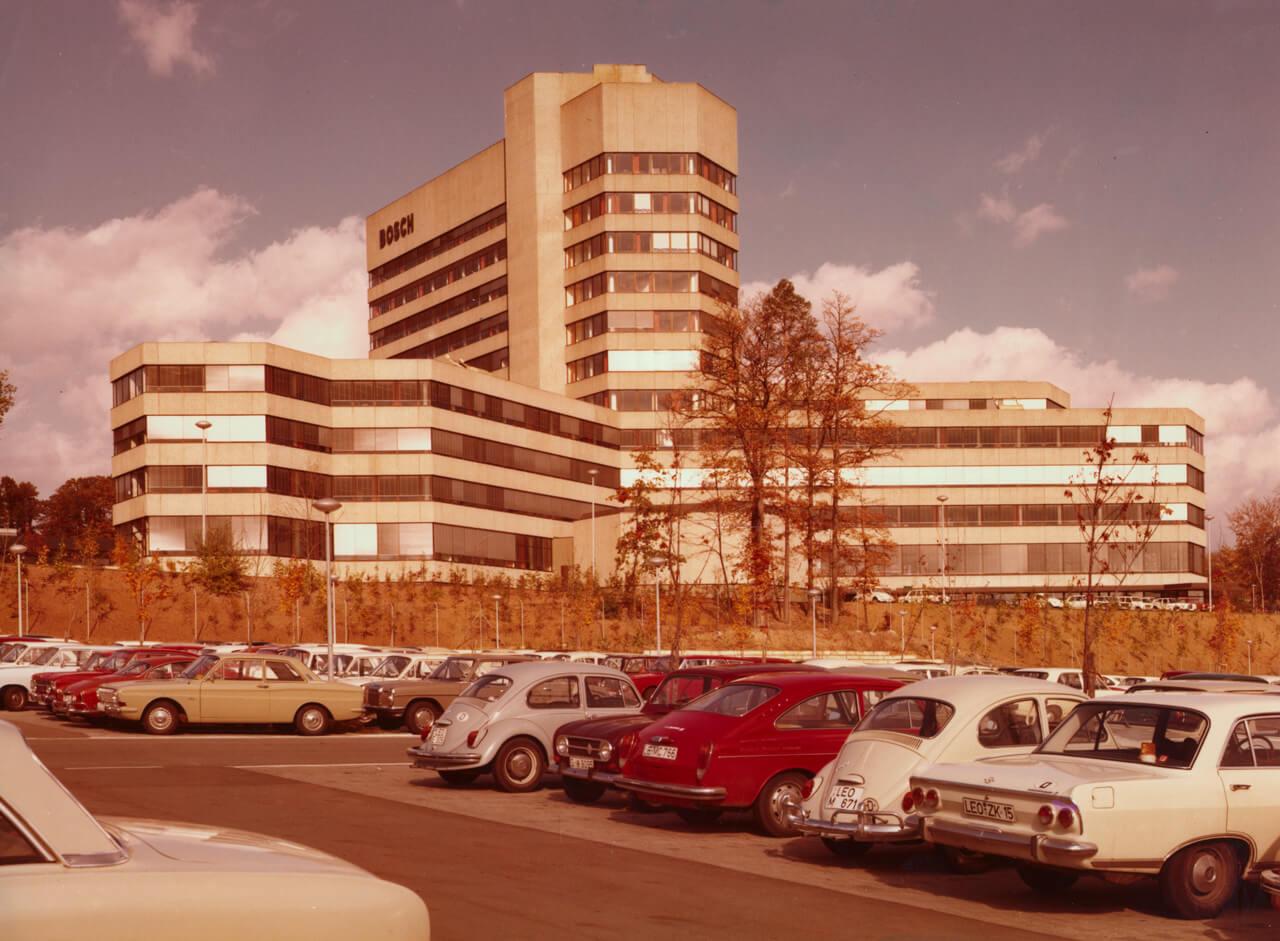
A fenti rugalmas összeszerelő rendszert azóta világszerte számos autó-, sőt egyéb gyárban is alkalmazták. Üzemeltetésének előnye az is, hogy hozzájárult a hardver- és szoftvermodulok folyamatos fejlesztéséhez, ami szintén előnyére vált cégünknek. Rég nyilvánvaló lett ugyanis, hogy az emberek és gépek közötti munkamegosztás és kommunikáció lesz a döntő és következő lépés a gyártástechnológiai fejlesztési folyamatában.
Ipar 4.0 és ami utána jön
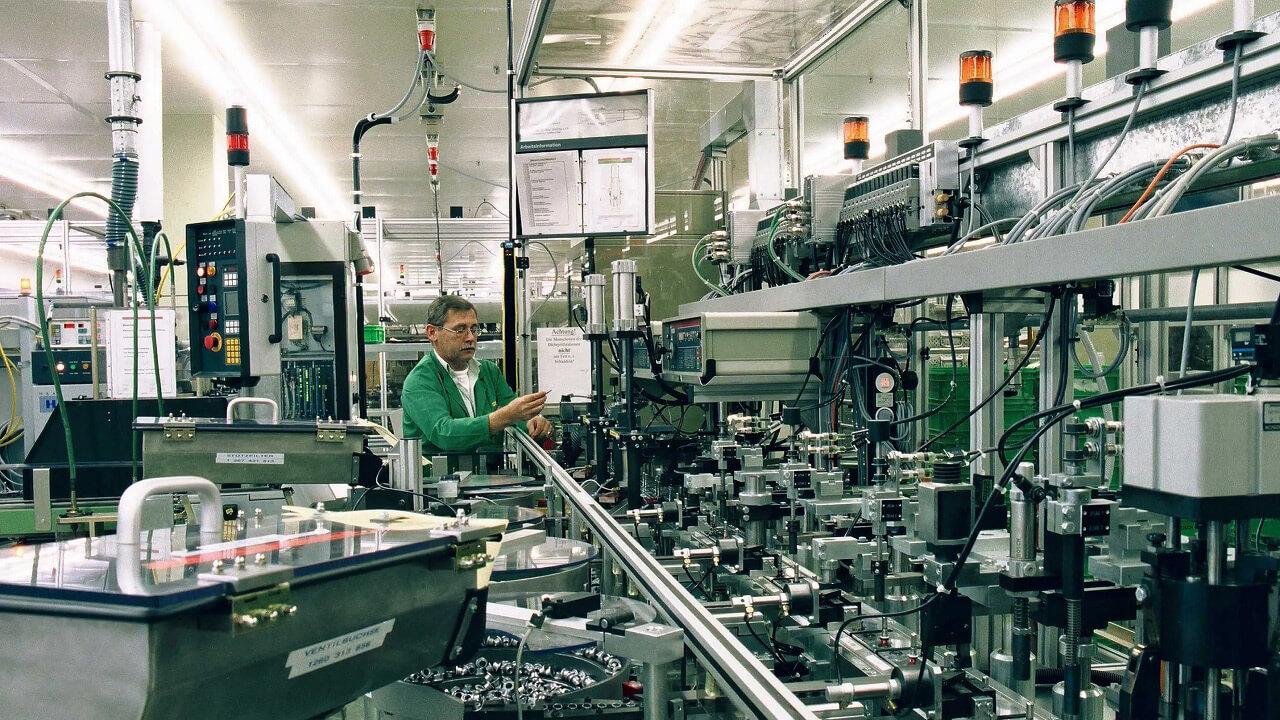
2011 -ben a bejegyzés elején ismertetett intelligens, összekapcsolt gyár koncepciója az „Ipar 4.0” hivatalos kifejezés megalkotásához vezetett. A fejlődés és az innováció persze folyamatos. Ennek köszönhetően növekedett az elmúlt évtizedekben a termelés. A Bosch üzemei, sőt maguk az autógyárak is egyre többet tudtak termelni, egyre jobb minőségben. Ma szinte minden vezető járműipari szereplő egységei egyet jelentenek a csúcstechnológiával. Ebben pedig nagy szerepe van a Bosch munkavállalóinak, akik sokszor mutattak irányt az elmúlt évtizedekben az egész iparágnak. Köszönjük nektek!